Lubricating grease is an essential component in maintaining machinery and equipment across various industries. It plays a crucial role in reducing friction, protecting surfaces from wear, and ensuring smooth operation. Understanding the intricacies of lubricating grease can significantly enhance the longevity and performance of your equipment.
Whether you're a mechanic, engineer, or simply someone interested in maintaining machinery, this comprehensive guide will provide you with all the necessary information about lubricating grease. From its composition and types to its applications and maintenance, we'll cover everything you need to know.
In today's fast-paced industrial world, choosing the right lubricating grease is more important than ever. This guide aims to equip you with the knowledge to make informed decisions and ensure your equipment operates at its best.
Read also:Pinay Sex Scandal News 2024
Table of Contents
- What is Lubricating Grease?
- Components of Lubricating Grease
- Types of Lubricating Grease
- Benefits of Using Lubricating Grease
- Applications of Lubricating Grease
- Choosing the Right Lubricating Grease
- Grease Application Methods
- Maintenance and Storage of Lubricating Grease
- Common Mistakes to Avoid
- Conclusion
What is Lubricating Grease?
Lubricating grease is a semi-solid lubricant designed to reduce friction between surfaces in relative motion. It is widely used in industrial machinery, automotive applications, and various other sectors. Unlike liquid lubricants, grease remains in place, providing a protective barrier that minimizes wear and tear.
Key Characteristics
Lubricating grease is characterized by its thick consistency, which allows it to adhere to surfaces and resist being squeezed out under pressure. This makes it ideal for applications where oil might leak or be insufficient.
How It Works
Grease works by forming a thin film between moving parts, reducing friction and preventing metal-to-metal contact. This not only prolongs the life of the machinery but also improves efficiency and reduces energy consumption.
Components of Lubricating Grease
Lubricating grease consists of three primary components: base oil, thickener, and additives. Each component plays a crucial role in determining the performance and properties of the grease.
Base Oil
The base oil constitutes the majority of the grease composition, typically around 70-90%. It provides the lubricating properties and determines factors such as viscosity and temperature resistance.
Thickener
The thickener gives grease its semi-solid consistency. Common thickeners include lithium, calcium, and clay. The choice of thickener affects the grease's stability, water resistance, and temperature range.
Read also:No Lube No Protection Copy Paste
Additives
Additives are included to enhance specific properties of the grease, such as anti-wear, corrosion resistance, and extreme pressure performance. These additives ensure the grease performs optimally under various conditions.
Types of Lubricating Grease
There are several types of lubricating grease available, each designed for specific applications and environments. Understanding these types can help you choose the right grease for your needs.
Lithium Grease
Lithium grease is one of the most common types, known for its excellent water resistance and wide temperature range. It is suitable for a variety of applications, from automotive to industrial machinery.
Calcium Grease
Calcium grease offers excellent water resistance and is often used in wet environments. However, it has a limited temperature range compared to lithium grease.
Synthetic Grease
Synthetic grease is formulated with synthetic base oils, providing superior performance in extreme temperature conditions. It is ideal for high-performance applications where traditional greases may not suffice.
Benefits of Using Lubricating Grease
Using lubricating grease offers numerous benefits that contribute to the efficient operation and longevity of machinery. Here are some key advantages:
- Reduces friction and wear between moving parts
- Protects against corrosion and rust
- Seals out contaminants such as dust and moisture
- Remains in place under pressure and vibration
- Extends the life of machinery and reduces maintenance costs
Applications of Lubricating Grease
Lubricating grease is used in a wide range of applications across various industries. Below are some common uses:
Automotive Industry
In the automotive sector, grease is used to lubricate wheel bearings, steering components, and other moving parts. It ensures smooth operation and reduces noise and vibration.
Industrial Machinery
Industrial machinery relies heavily on grease to maintain optimal performance. From conveyor belts to gears and bearings, grease plays a critical role in reducing downtime and improving efficiency.
Construction Equipment
Construction equipment operates in harsh conditions, making grease an essential component for protecting components from wear and environmental factors.
Choosing the Right Lubricating Grease
Selecting the appropriate lubricating grease is crucial for ensuring optimal performance and longevity of your equipment. Consider the following factors when making your choice:
Operating Temperature
Ensure the grease can withstand the temperature range of your application. Some greases are formulated for high-temperature environments, while others are better suited for low temperatures.
Load and Speed
The load and speed of the application affect the type of grease required. Heavy loads and high speeds may necessitate greases with extreme pressure additives.
Environmental Conditions
Consider the environmental conditions in which the grease will be used. For example, water-resistant greases are ideal for wet environments, while synthetic greases are better for extreme temperatures.
Grease Application Methods
Proper application of lubricating grease is essential for maximizing its effectiveness. Here are some common methods:
Manual Application
Manual application involves using a grease gun to apply grease directly to the desired area. This method is suitable for small-scale applications and requires precision.
Automated Systems
Automated grease application systems are used in large-scale operations to ensure consistent and accurate lubrication. These systems can be programmed to apply grease at regular intervals.
Maintenance and Storage of Lubricating Grease
Proper maintenance and storage of lubricating grease are vital for maintaining its quality and effectiveness. Follow these guidelines:
Regular Inspection
Regularly inspect machinery for signs of grease degradation, such as discoloration or hardening. Replace grease as needed to prevent damage to components.
Storage Conditions
Store grease in a cool, dry place away from direct sunlight and extreme temperatures. Ensure containers are sealed tightly to prevent contamination.
Common Mistakes to Avoid
Avoiding common mistakes can significantly improve the effectiveness of lubricating grease. Here are some pitfalls to watch out for:
- Using the wrong type of grease for the application
- Over-greasing, which can cause excess heat and pressure
- Ignoring contamination, which can lead to premature wear
- Failing to follow manufacturer recommendations for application and maintenance
Conclusion
Lubricating grease is an indispensable component in maintaining machinery and equipment across various industries. By understanding its composition, types, and applications, you can make informed decisions to ensure optimal performance and longevity of your equipment.
We encourage you to share your experiences and insights in the comments section below. Additionally, explore our other articles for more valuable information on machinery maintenance and lubrication. Together, let's keep the world moving smoothly!
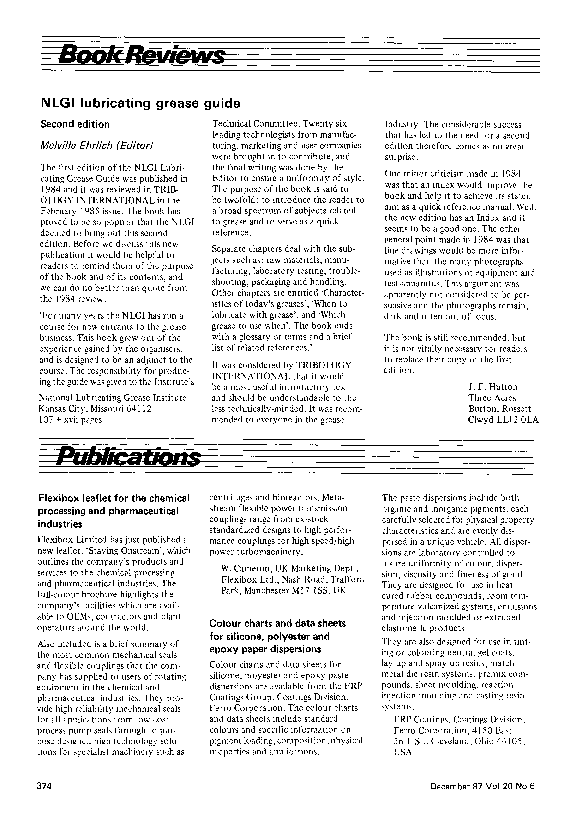
